Research at CoTide
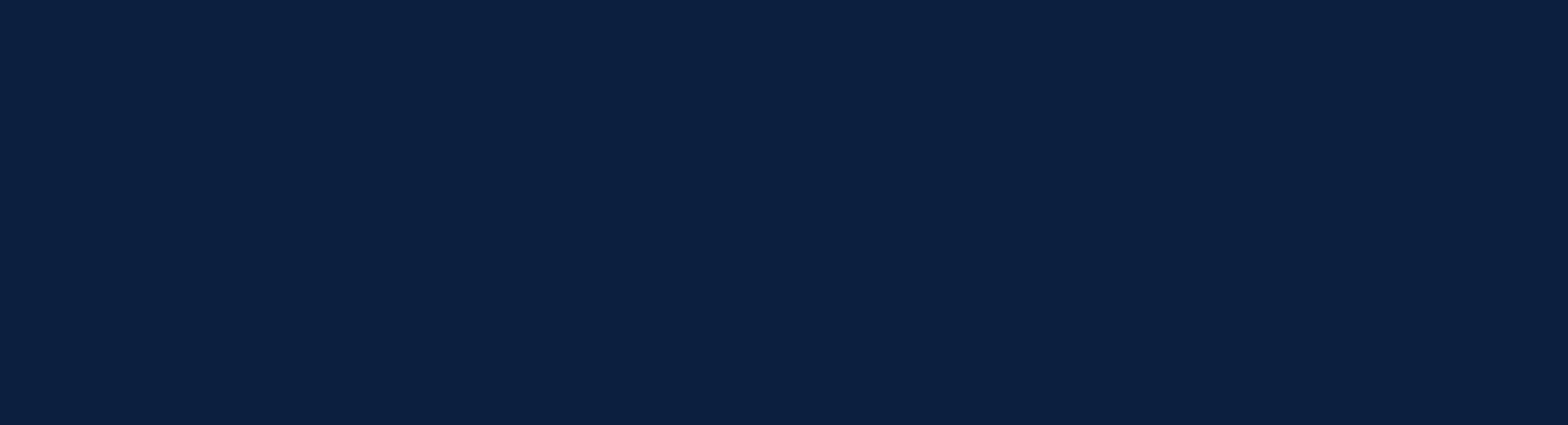
Research Challenges
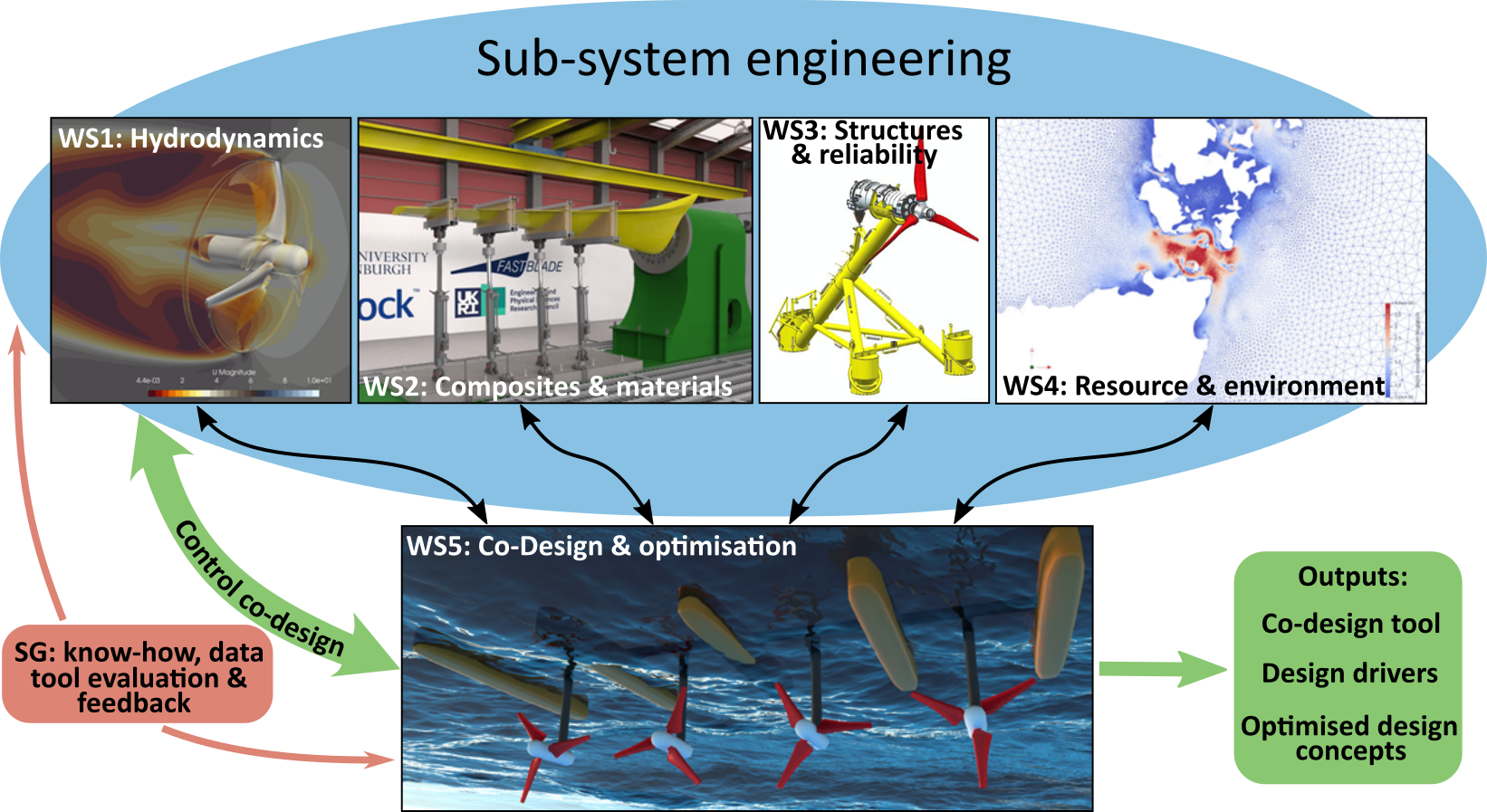
CoTide consists of five inter-related workstreams that bring together tightly-coupled tidal stream energy sub-systems which are integrated and interact through control co-design in order to deliver new co-design tools, understanding of important design drivers and optimised design concepts. This process is supported by our stakeholder group, consisting of 25 partners.
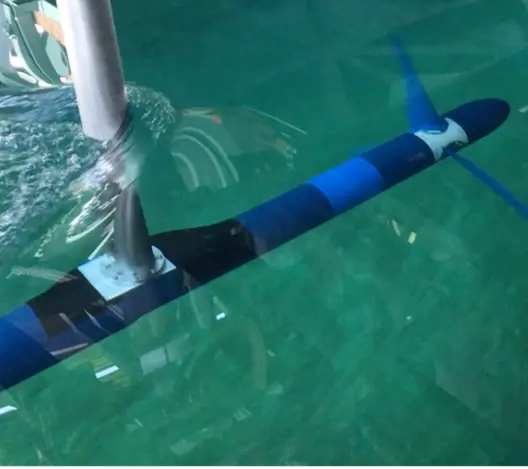
Work Stream 1
Device Hydrodynamics
Hydrodynamic design that considers multiple design and loading scenarios requires efficient, robust and accurate engineering models. We will develop fluids models for tidal rotors and fixed and floating systems in the complex flows experienced by tidal turbines. Key challenges already identified by industry partners include integrating blockage in engineering models and exploiting the proven performance advantages this can offer; understanding how waves, turbulence, vertical and lateral shear lead to unsteady blade loading; understanding and minimising cavitation limits; understanding and utilising blade hydroelasticity to attenuate loads; how turbine design, operation and control (maximum thrust) inform the design of fixed and floating support structures (pitch and surge motions). To support the development of the required engineering tools and identify the relevant flow physics, we will use advanced simulation methods together with high quality large-scale lab experiments.

Work Stream 2
Composites & Rotor Materials
Composite tidal stream blades carry greater thrust loads over much shorter lengths than wind turbine blades, with much sharper reductions in laminate thickness, constituting a fundamental unknown in the fatigue/failure design of blades. Wave loading, turbulence, cavitation and leading-edge erosion from seawater and sand complicate design, increase uncertainty and cost of blade design and manufacture. In addition, significant interactions exist between design parameters (e.g. selection of material and geometry influences manufacturing method and fatigue performance) which are not appropriately considered in current blade designs. We will: fatigue test composite blades at full scale for the first time in the FastBlade structural fatigue testing facility with realistic hydrodynamic loads from fluids models and experiments (WS1) and ocean observations (WS4); develop an integrated blade design tool and provide pathways for certification of composite blades and rotors; develop a circular economy materials approach; design, manufacture and test a full-scale recyclable, thermoplastic or bio-based composite tidal blade.

Work Stream 3
Structures & Reliability
Reliability and resilience are critical for tidal energy, with offshore interventions inherently unsafe, installation and retrievals expensive, and poor access for inspection, repair and maintenance. WS3 addresses materials and structures to ensure reliability subject to fatigue, corrosion, abrasion and impact loading and environmental conditions in a cost-effective, environmentally cognisant manner. Materials, structures and structural integrity solutions, including adaptive, smart, damage tolerant and self-repair mechanisms, will be investigated, guided by co-design, as part of an integrated reliability-driven structural solution. Design considerations include primary function, manufacturability (including local resources and constraints), the environment and safety
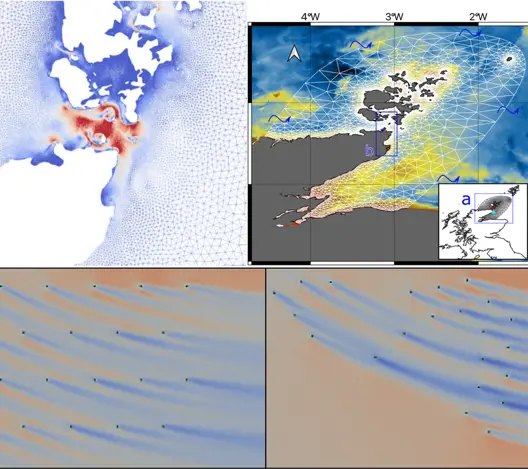
Work Stream 4
Metocean, Resource & Environment
Hydrodynamic, structural and operational design are tightly coupled to the harsh environment. The yield of a tidal farm is a function of all of these and an accurate assessment of yield is vital for developers. The ocean environment is stochastic and multi-scale, difficult to model, expensive to measure and is modified by the presence of turbines. WS4 will work with other WS to define essential measurements to inform turbine design, and will develop exemplar sites that capture the diversity of site characteristics. We will refine turbine feature and wake representation within multi-scale hydrodynamic and reduced order models. Yield analysis, resource optimisation and environmental impact modelling will use idealised and real-world case studies where field data can validate modelling, and will be informed from device and structural models.
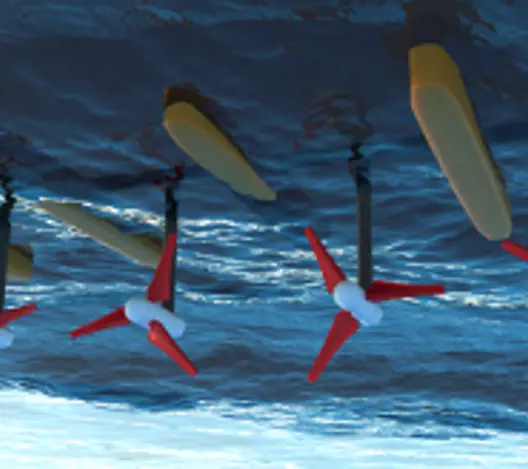
Work Stream 5
Co-design & Optimisation
Engineering models from WS1-4 will be integrated to deliver whole system co-design tools, which we will use to explore how design and control of operation can be used to balance objectives. Performance, non-cost and cost-surrogate metrics will be used to define objective functions that will be used to balance lifetime energy yield with durability, resilience, complexity, system weight, and environmental and ecological impact. Through optimisation and machine learning techniques, control co-design will be used to understand, test sensitivity to, and optimise around key design drivers and objectives. Through this process of interconnected work streams, we will deliver reliable co-design tools to provide efficient and robust engineering models, understand the role of key design drivers, and optimised design solutions for different environments and objectives.
